Following a strong history in well-testing in the oil and gas industry, ScanTech Offshore took the decision to diversify and enter the renewables sector. Relying on existing expertise in engineering and a passion for the energy sector ScanTech Offshore quickly became the go to supplier of compressed air for big bubble curtains.
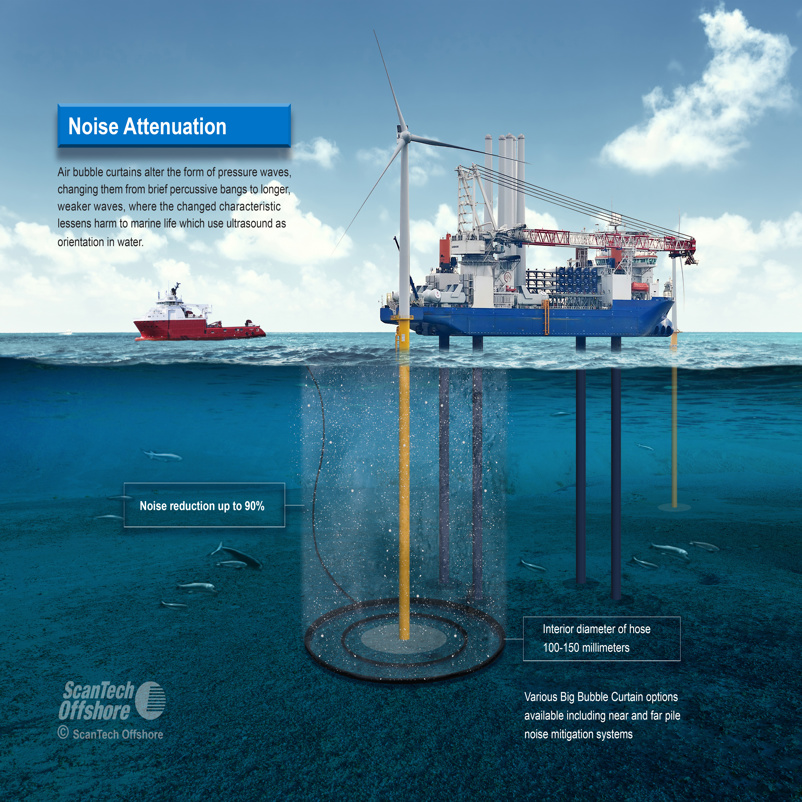
The big bubble curtain
The big bubble curtain was developed as a compressed air system for sound absorption in water and especially protects porpoises and seals which use ultrasound as orientation in water. Ordinary construction noises travel much more easily underwater, and sound levels can be five times higher than in open air. This can be enough to harm and even kill sea life. However, air bubbles resonate in response to sound, absorbing the energy. When formed into a curtain they reflect the sound, effectively keeping it within the curtained area.
A ship is typically fitted with a set of ScanTech Offshore air compressors to deliver compressed air to a flexible tube with special nozzle openings. The tube is installed on the seabed around the locations where the sound is generated, and the compressed class zero air creates the bubble curtain through the nozzle openings.
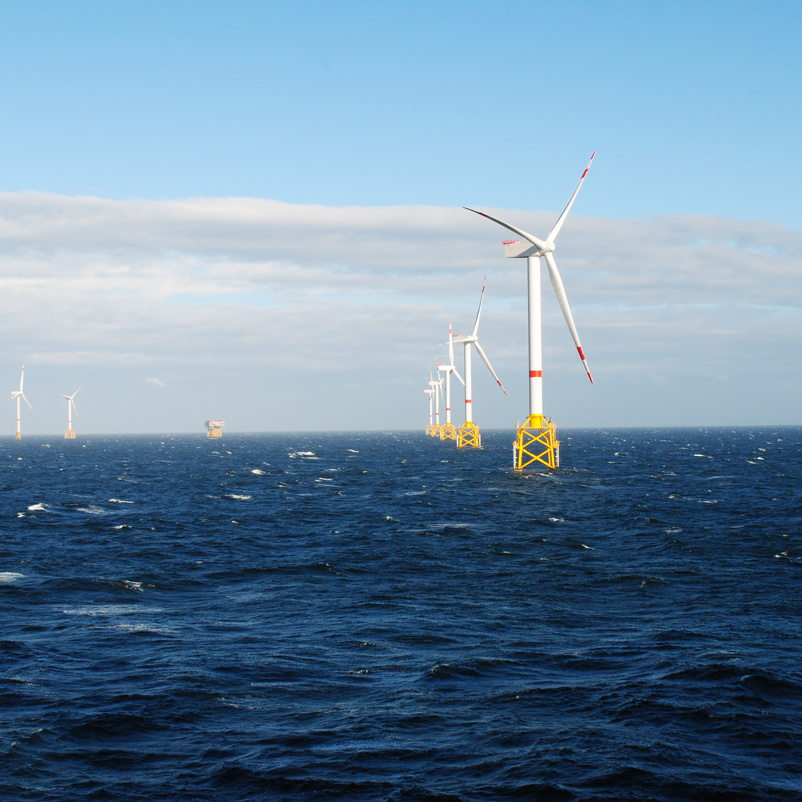
A powerful partnership with HydroTechnik Lübeck
For the last two years, ScanTech Offshore has partnered with HydroTechnik Lübeck, a leading German company that has been pioneering specialised bubble curtain technology to support wind farm construction projects. Together, its stackable air compressors and SeaSentry filtration system supply the huge volumes of clean ‘class zero’ compressed air required.
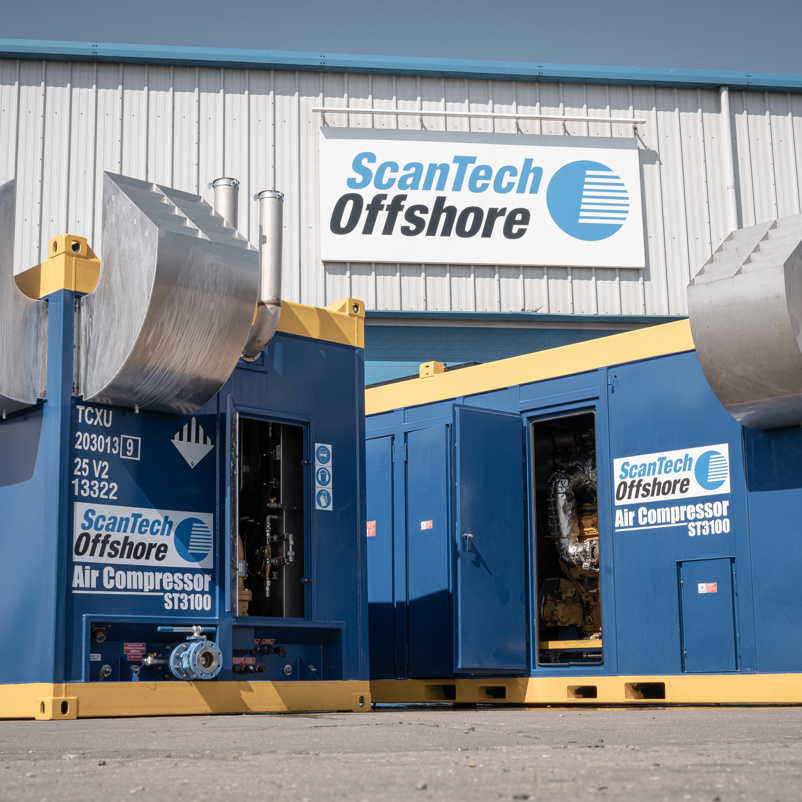
The ST3100 air compressor
The world’s first and only air compressors designed specifically for big bubble curtain projects. The ST3100 air compressors utilise a Caterpillar engine and a ScanTech Offshore original radiator technology, providing the air required to create a bubble curtain that reduces noise by up to 90%.
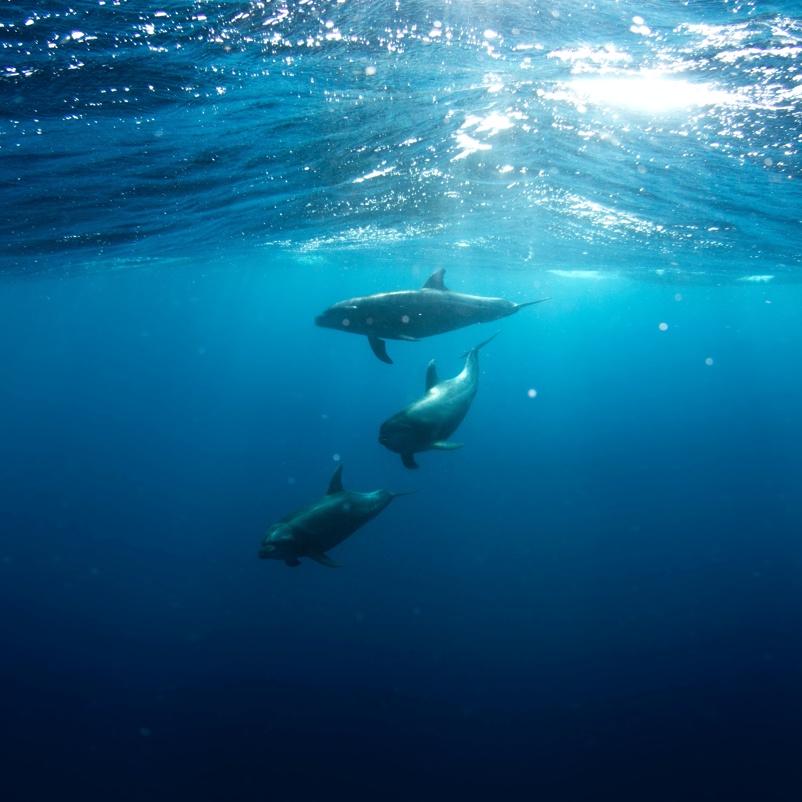
Protection of marine life
The team will provide a double layer of sound protection to marine life in the area, equipping a large noise mitigation vessel with sufficient air compressors to create a double big bubble curtain around the monopile. In addition, electric air compressors will be located onboard the heavy lift/pile driving installation to provide air for a further, smaller near pile bubble curtain, providing additional noise attenuation during the installation of the monopile foundations.
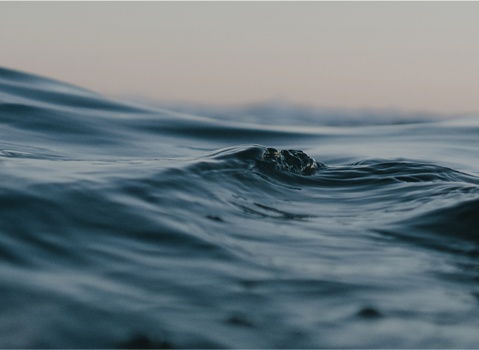